Advanced Fasteners and Machining Techniques for Custom-made Production
Browsing the Globe of Fasteners and Machining: Strategies for Accuracy and Rate
In the complex realm of fasteners and machining, the pursuit for precision and speed is a perpetual difficulty that demands careful focus to information and strategic planning. From comprehending the diverse range of fastener kinds to selecting optimum materials that can endure rigorous needs, each action in the process plays a critical function in accomplishing the wanted outcome.
Understanding Fastener Types
When choosing fasteners for a project, comprehending the numerous types readily available is important for ensuring ideal efficiency and reliability. Bolts are made use of with nuts to hold materials together, while screws are functional bolts that can be utilized with or without a nut, depending on the application. Washing machines are essential for distributing the lots of the bolt and preventing damage to the material being attached.
Selecting the Right Materials
Comprehending the importance of choosing the appropriate materials is critical in making certain the optimum performance and dependability of the selected bolt types reviewed formerly. When it comes to bolts and machining applications, the product option plays an important function in establishing the overall strength, toughness, deterioration resistance, and compatibility with the desired environment. Different materials offer varying homes that can substantially influence the efficiency of the bolts.
Usual materials made use of for fasteners consist of steel, stainless steel, aluminum, brass, and titanium, each having its special strengths and weak points. Steel is renowned for its high toughness and longevity, making it appropriate for a vast variety of applications. Picking the best product involves taking into consideration elements such as stamina needs, environmental problems, and budget restrictions to ensure the preferred performance and durability of the bolts.
Accuracy Machining Techniques
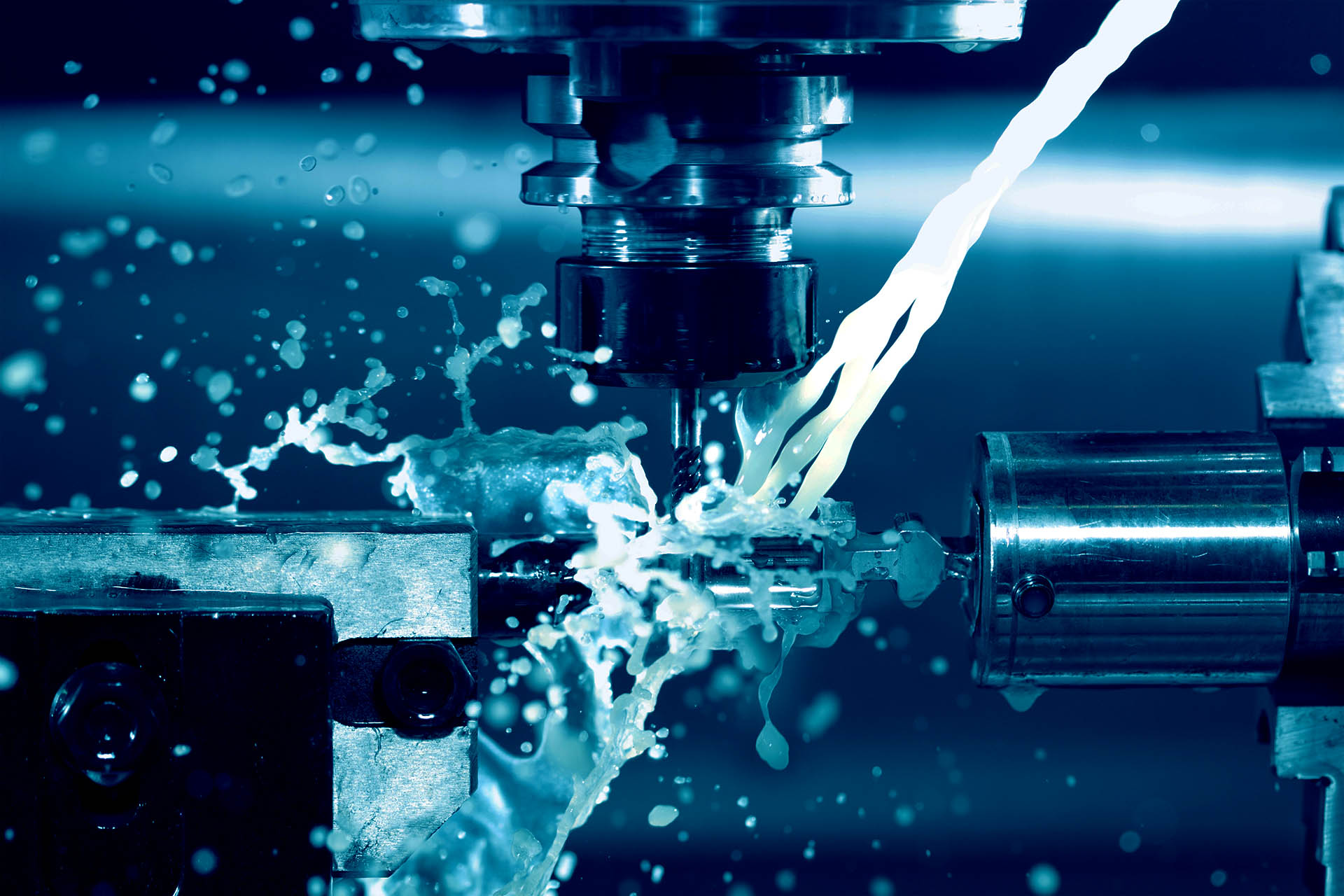
Along with CNC machining, various other precision strategies like grinding, turning, milling, and exploration play important duties in fastener production. Grinding aids achieve great surface area finishes and read this article limited dimensional resistances, while transforming is frequently made use of to create cylindrical parts with accurate diameters. Milling and exploration operations are necessary for forming and creating holes in fasteners, guaranteeing they fulfill exact specs and feature correctly.
Enhancing Speed and Efficiency
To maximize fastener manufacturing processes, it is necessary to enhance operations and carry out efficient methods that complement accuracy machining techniques. Automated systems can manage repetitive tasks with precision and rate, allowing employees to focus on more facility and value-added activities. By incorporating these techniques, suppliers can achieve a balance in between speed and precision, ultimately improving their affordable edge in the fastener market.
Top Quality Control Steps
Implementing rigorous high quality control measures is crucial in making sure the reliability and consistency of fastener items in the manufacturing process. Quality control procedures incorporate various stages, beginning with the option of resources to the final assessment of the ended up fasteners. One basic aspect of high quality control is performing complete material assessments to validate conformity with specs. This entails assessing factors such as material durability, strength, and make-up to guarantee that the bolts fulfill sector requirements. In addition, keeping track of the machining processes is necessary to maintain dimensional precision and surface area finish quality. Utilizing innovative modern technology, such as computerized assessment systems and precision measuring tools, can boost the precision and effectiveness of quality control procedures.
Regular calibration of equipment and equipment is vital to keep consistency in manufacturing and ensure that fasteners fulfill the required resistances. Implementing strict methods for identifying and attending to defects or non-conformities is essential in preventing substandard products from getting in the marketplace. By establishing a thorough quality control framework, suppliers can copyright the track record of their brand name and supply fasteners that meet the greatest criteria of performance and sturdiness.
Conclusion

In the elaborate realm of fasteners and machining, the quest for precision and speed is a continuous obstacle that requires meticulous attention to information and strategic preparation. When it comes to bolts and machining applications, the product option plays a critical duty in determining the overall strength, resilience, corrosion resistance, and compatibility with the intended environment. Accuracy machining entails different sophisticated approaches that make sure the limited tolerances and specifications required for bolts.In enhancement to CNC machining, various other precision techniques like grinding, transforming, milling, and exploration play crucial functions in fastener production.To optimize fastener production procedures, it is necessary to improve operations and execute efficient methods that complement precision machining strategies.